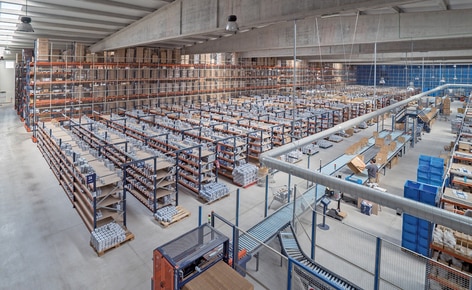
Innovación y agilidad en la preparación de pedidos de venta ‘online’ de suministros industriales, ferretería y bricolaje
Nuevo centro logístico de Cofan sectorizado en distintas áreas y orientado al picking
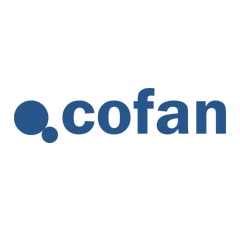
Cofan ha construido un moderno centro logístico sectorizado en distintas áreas que organizan la mercancía en función de sus características y el nivel de demanda. Mecalux ha suministrado todos los sistemas de almacenaje de la instalación (incluido un almacén automático miniload) y un completo circuito de transportadores con estaciones de preparación de pedidos, conformadoras de cajas, precintadoras, básculas y rampas de clasificación. Esta solución permite que el picking se realice con agilidad y de forma eficiente.
Quién es Cofan
Cofan es una empresa con más de 15 años de experiencia en el desarrollo y venta electrónica de productos de suministro industrial, ferretería y bricolaje. Dispone de tres marcas distintas (Cofan, Bricofan y Cofan Home) que se comercializan en más de 12 países.
La compañía se propone reforzar su ritmo de crecimiento gracias a la innovación y la introducción de la tecnología en todos sus procesos productivos. Actualmente, Cofan representa un referente del sector industrial y la automoción, así como en una marca de confianza de distribución online.
Necesidades de Cofan
El fuerte crecimiento experimentado en los últimos años obligó a Cofan a construir un nuevo centro logístico que tuviera presente las previsiones de expansión a corto y medio plazo.
La empresa necesitaba obtener la máxima capacidad de almacenaje y clasificar los productos por tipo de referencia con el fin de agilizar la preparación y consolidación de los pedidos. También requería minimizar los costes de explotación y garantizar un servicio eficiente para los usuarios de su e-commerce.
Solicitó la colaboración de Mecalux para encontrar una solución idónea que se adaptara a todos los requisitos presentados, permitiera incrementar el número de expediciones diarias y, además, mejorara los plazos de entrega de los pedidos. El proyecto era todo un reto, debido a la diversidad de productos de tamaños, pesos y clasificaciones distintas en base a los criterios de rotación ABC, lo que exigía un análisis muy detallado de cada uno de ellos.
El centro logístico
El resultado es este nuevo centro logístico, localizado en la población de Campo de Criptana, a una distancia de 150 km de Madrid, y muy cercano a las principales plataformas logísticas de la península. Se halla en un importante nudo de comunicaciones que facilita la óptima distribución de los productos por toda la geografía española.
El almacén de 25.000 m2 está sectorizado en distintas áreas según los requerimientos de la empresa, lo que permite clasificar cada familia de productos en función de su nivel de demanda y sus dimensiones. La operativa principal es el picking, con muchos pedidos y pocas líneas de preparación por cada uno de ellos.
Estas son las distintas partes y sectores del almacén:
- Almacén de picking manual de gran consumo
- Almacén de reserva
- Almacén de reserva y picking de productos voluminosos
- Almacén automático miniload
- Almacén de producto sensible
- Conformadoras automáticas de cajas de cartón
- Circuito de transportadores y mesas de preparación
- Zona de consolidación y control
- Zona de clasificación de pedidos
Picking: la función principal del centro logístico
Por las características y la tipología de los pedidos, la parte central del almacén se ha destinado a los productos de mayor consumo. Esta zona requería una gran accesibilidad –a la vez que flexibilidad–, con un número de operarios variable en función de la demanda y la franja horaria.
Para cumplir este objetivo, se han instalado estanterías de poca altura con una capacidad de referencias limitada. Los palets de reserva de estos productos se encuentran en las estanterías situadas a ambos lados del área de picking y la reposición se realiza aprovechando las horas valle, es decir, cuando hay un menor trabajo de preparación de pedidos.
Por el centro de esta zona discurre el circuito de transportadores que se desplazan a una velocidad de 45 m/min y al que se han adosado, a ambos lados, seis mesas de rodillos de gran capacidad para la preparación de los pedidos.
Conformadora de cajas
Todo el proceso se inicia con la conformación de cajas. Esta tarea la realizan cuatro máquinas automáticas (cada una de ellas destinada a un tamaño distinto) ubicadas al comienzo del circuito de transporte.
El software de gestión de almacenes (SGA) comunica a las conformadoras la cantidad de cajas y el tamaño que requieren los pedidos, teniendo en cuenta la composición de cada ola de preparación. Las cajas, identificadas mediante la asignación y pegado de una etiqueta, se dirigen progresivamente por el circuito de transporte hasta la primera mesa de preparación, donde se halla el producto necesario para su pedido. El operario lee la etiqueta del paquete con un terminal de radiofrecuencia para conocer el material que debe introducir.
Almacén de picking manual
A cada una de las seis mesas de preparación le corresponde una zona con un número determinado de estanterías. Los operarios recorren los pasillos de las estanterías utilizando carros para recoger las referencias que el SGA ha indicado a través del terminal de radiofrecuencia.
Una vez finalizada esta fase, el pedido se devuelve a la cinta para ser trasladado hasta la siguiente estación que contiene los productos que precisa. En el caso de haberse completado, el transportador lo encamina automáticamente hasta la zona de consolidación y clasificación.
Almacén automático miniload
Después de esta zona de gran rendimiento, se encuentran las mesas de preparación anexas al almacén automático de cajas miniload. En esta área se ubican los productos de poco tamaño y menor consumo (básicamente tipo B y C).
El consumo de estos productos cumple el principio de Pareto, o regla del 80/20, es decir, el 80% de las referencias tan solo suponen el 20% de los movimientos del almacén.
Almacén de producto sensible
Seguidamente, el circuito se dirige hasta las estanterías de paletización convencional en las que se depositan los productos voluminosos y de menor demanda. Justo al lado, el almacén de producto sensible constituye la última fase del circuito.
Finalización
Los pedidos completados se trasladan hasta la zona de consolidación, donde se lleva a cabo el embalaje, etiquetado y la emisión de la documentación requerida para su expedición.
Teniendo en cuenta las necesidades de la compañía, y debido a la gran cantidad de pedidos por jornada que se elaboran, en esta área se han previsto dos conjuntos de básculas, precintadoras y etiquetadoras totalmente automáticas.
Una vez superada la zona de consolidación, los pedidos terminados se dirigen hacia las cinco rampas de clasificación ubicadas delante de los muelles de carga. Allí se agrupan por rutas y agencias antes de ser expedidos.
Almacén miniload
En el almacén automático para cajas se alojan los productos de menor tamaño y baja rotación. En esta zona del centro logístico, donde se realiza la preparación de pedidos de acuerdo con el principio de “producto a hombre”, se han instalado dispositivos put-to-light que agilizan la operativa y minimizan los errores de la gestión manual.
Hay dos puestos de picking en los que los operarios reciben las cajas procedentes del almacén y, a su espalda, una mesa de preparación de pedidos con capacidad para olas de once pedidos a la vez.
Los transelevadores colocan los contenedores (eurocajas) con la mercancía en los transportadores, que los conducen automáticamente hasta los puestos de picking. Los operarios extraen los productos que les indica el sistema en una pantalla y los depositan en la caja de cartón correspondiente en la mesa de preparación de pedidos.
Los monitores put-to-light guían visualmente a los operarios mediante tres colores diferentes, que les señalan dónde deben dejar cada artículo. El trabajador pulsa el indicador para confirmar que ha ejecutado la acción.
El almacén automático está compuesto por tres pasillos con estanterías de simple profundidad a ambos lados. Las estanterías disponen de 19 niveles, que alcanzan una altura de 8,6 m.
Por cada pasillo circula un transelevador miniload de tipo monocolumna que se encarga de gestionar las entradas y salidas de la mercancía. Estas máquinas trabajan a una velocidad de traslación de 180 m/min y 100 m/min en elevación.
El transelevador está equipado con un sistema de extracción de palas, que se introducen por la parte inferior de las cajas y las extraen o sitúan en las ubicaciones a ambos lados del pasillo.
En la parte posterior de los pasillos se ha habilitado un área de mantenimiento con puertas de acceso seguro que velan por la seguridad de los operarios. Los transelevadores se dirigen ahí cuando requieren alguna intervención o reparación.
Easy WMS de Mecalux
El almacén de picking automático está gestionado por el software de gestión de almacenes Easy WMS de Mecalux, que se encarga de controlar y coordinar su correcto funcionamiento.
Este potente sistema realiza distintas operaciones, entre las que se incluyen la asignación de ubicaciones y almacenaje de las cajas según su rotación, extracción de la mercancía y preparación de pedidos.
Easy WMS de Mecalux está en comunicación permanente y bidireccional con el SGA general del almacén y el ERP de Cofan, transfiriéndose datos e información para lograr la máxima productividad y rentabilidad del picking.
Distintos sistemas de almacenaje
La distribución de los distintos sistemas de almacenaje instalados en el centro logístico se ajusta a la gran variedad de productos disponibles y tiene en cuenta su demanda y rotación; lo que permite agilizar la preparación de pedidos.
En la parte central, donde se alojan los productos de mayor consumo y menor tamaño, se han instalado 59 estanterías de picking de 2,5 m de altura y 2,7 m de longitud formadas por tres y cinco niveles con estantes.
Los pasillos tienen la suficiente anchura para que los operarios circulen con agilidad y sin interferencias. Un terminal de radiofrecuencia conectado con el SGA del almacén permite identificar y clasificar los productos. Los pedidos se preparan por olas, es decir, varios pedidos a la vez con el fin de optimizar al máximo el recorrido a lo largo de las ubicaciones dentro de la instalación.
Alrededor de la zona destinada al picking manual de gran consumo, se han instalado estanterías de paletización convencional de 7,5 m de altura. En ellas se almacena la mercancía de gran volumen y la reserva de los productos de alta rotación en palets. También se efectúa picking directamente sobre los niveles inferiores.
Los operarios utilizan preparadoras de pedidos de baja cota, ya que están adaptadas para hacer picking en una posición ergonómica y pueden trasladar hasta dos palets a la vez.
Se ha habilitado un paso inferior que cruza transversalmente las estanterías y cumple la función de salida de emergencia, además de facilitar el flujo de mercancía. Los módulos de la parte superior del paso de seguridad están rejados para evitar la caída de materiales.
Beneficios para Cofan
- Alta capacidad de almacenaje: el nuevo centro logístico de 25.000 m2 de Cofan está equipado con distintos sistemas de almacenaje que se adaptan a su amplia variedad de productos, con dimensiones muy distintas.
- Eficiente sistema de preparación de pedidos: la distribución de la mercancía, teniendo en cuenta sus características y demanda, permite optimizar los movimientos de los operarios y rentabilizar al máximo la preparación de pedidos.
- Gestión eficiente: la combinación de los distintos softwares que intervienen en la instalación, tanto de gestión como de control, junto con el ERP de Cofan, extraen el máximo partido de todos los recursos.
Almacén convencional de Cofan, Ciudad Real | |
---|---|
Capacidad de almacenaje: | 7.824 palets |
Peso máximo por palet: | 800 kg |
Altura de las estanterías: | 7,5 m |
Galería
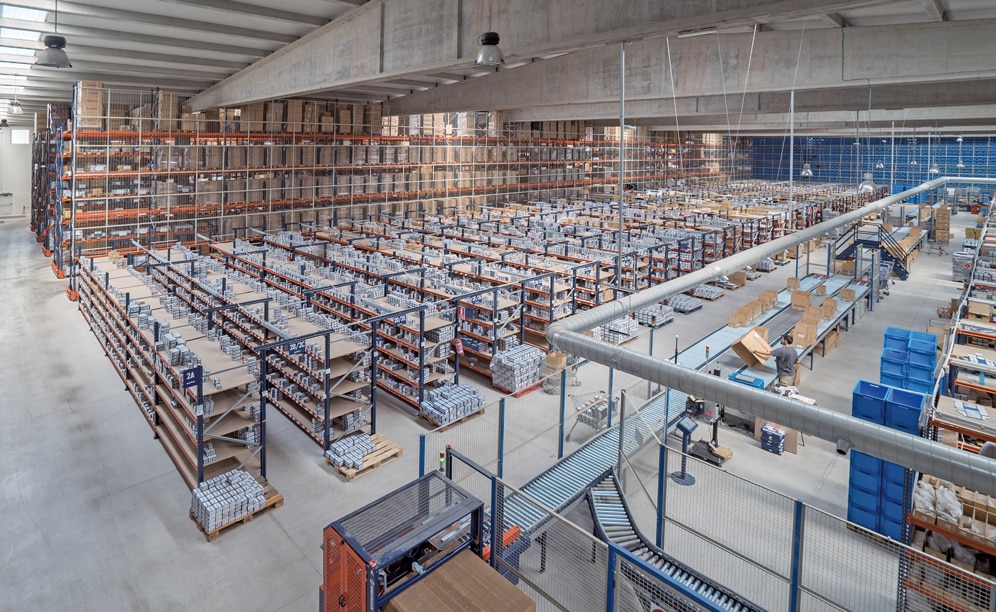
Mecalux ha suministrado todos los sistemas de almacenaje de la instalación: un almacén automático miniload, un completo circuito de transportadores con estaciones de preparación de pedidos, conformadoras de cajas, precintadoras, básculas y rampas de clasificación
Consulte con un experto